Introduction
In the last years, Powder Bed Fusion (PBF) has become one of the most important additive manufacturing solutions. The prediction of microscopic effects of the process has become one of the most important research activities. One of the most diffused simulation approaches is based on the Finite Element Method (FEM) including phase and material properties change and allowing to predict temperature gradients and residual stresses raising during melting/solidification process.
Methods
We have set up an uncoupled thermo-mechanical FEM approach based on sequential element activation. First, the thermal analysis is carried out to evaluate temperature distribution evolution when the heat source is moving on the powder bed; then the obtained temperature field is used as forcing term for the mechanical analysis. Finally, residual stresses and part displacements are evaluated. The heat source is approximated with a Goldak distribution and the heat source movements are tracked following the informations contained in the Gcode file which manages the printing process. Before melting, physical and mechanical properties correspond to the material at powder state, while, after re-solidification they correspond to the material at solid state.
Some results
Influence of process parameters on temperature and residual stresses evolution on a microscopic domain. The temperature history on a specific point of the domain, obtained with two combinations of laser power and spot radius is presented. The two combinations give rise to a similar energy density and a similar temperature evolution.
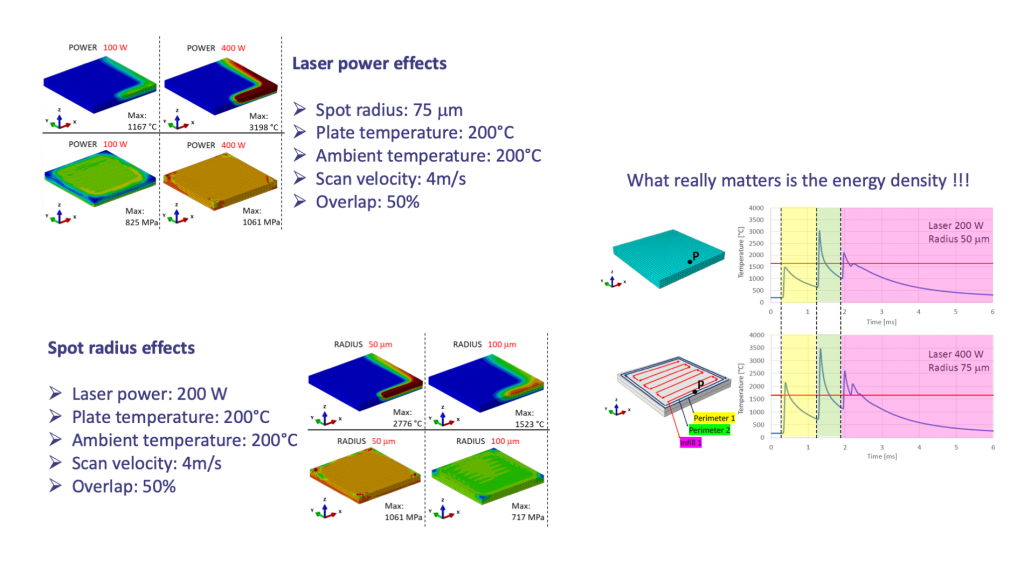
Outgoings
- Include in the model a pulsed laser heat source
- Include the effects of gas flow rate and direction to better simulate the cooling process